Cherryville, North Carolina, plant combines human hands, technology to supply covers used in company’s domestic upholstery line
CHERRYVILLE, N.C. — Here in this community of just over 6,000 people is a facility that is one of the most important assets — next to its people — in Hooker Furnishings’ domestic upholstery supply chain.
With a team of 63 workers, the company’s 50,000-square-foot cut-and-sew plant here marks, cuts and sews leathers and some fabrics for covers used the company’s Bradington-Young and M upholstery lines.
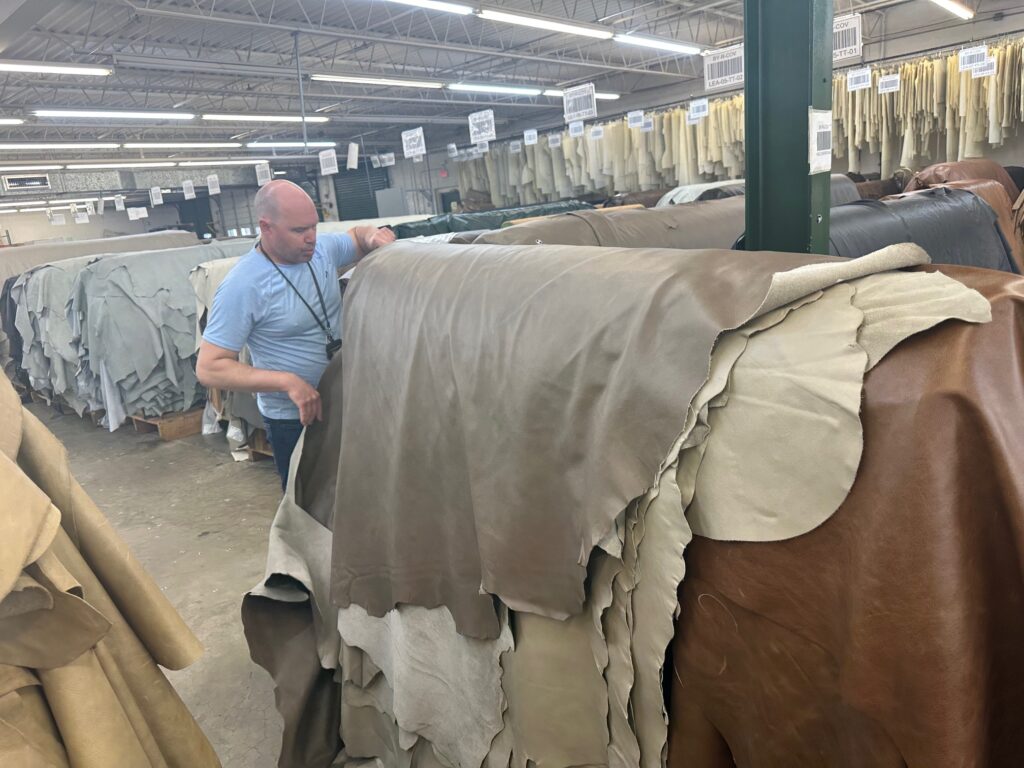
The facility uses some machinery in the process, including a Lectra cutting machine it acquired about five years ago that cuts multiple patterns on multiple finished hides at once, creating an efficiency and consistency that deliver the quality that retailers and consumers alike expect from the line. This includes finished leathers that are increasingly popular on sectionals, a growing part of the line.
However, the aniline hides that are the most natural in appearance of all the leathers because of their individual coloration and texture, are inspected, marked and cut —and eventually sewn — by a group of workers that collectively involves many hundreds of years of experience.
“The good thing about natural leathers is that you have a unique piece of furniture because no two of them are going to be the same. But you also have a consumer that wants a certain color because it’s going to match my rug and my drapes and everything in the room, said Cheryl Sigmon, vice president of merchandising at Bradington-Young, of the two types of products produced at the plant.
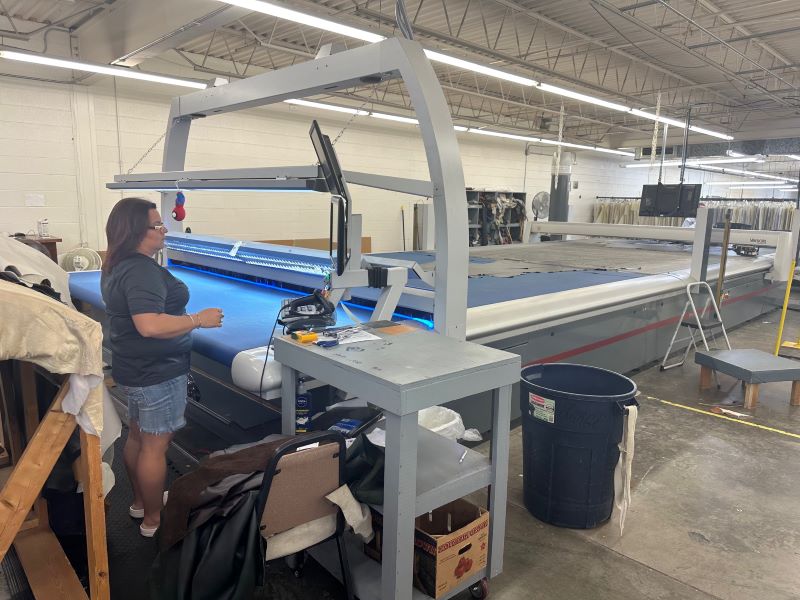
Whether by hand or through the use of machinery, the team at the cut-and-sew operation creates a finished product that ultimately covers frames produced at the company’s nearby plant in Hickory.
Home News Now saw the operation in person this past summer during a tour of the facilities led by Sigmon and Conrad Kerley, vice president of quality and cover operations at Bradington-Young. It’s an all-hands-on-deck process that requires experienced eyes and hands to inspect, cut and eventually sew the patterns that go into finished product, ranging from stationary and motion sofas and accent chairs to a wide mix of stationary and reclining sectionals in different configurations.
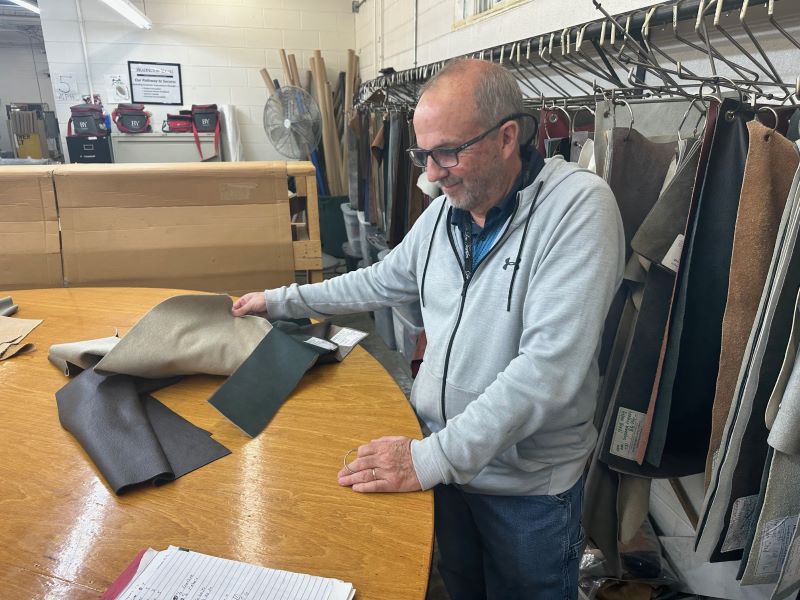
At any given time, there are as many as 19,000 hides in stock, roughly half of which are finished leathers. Thus, plenty of material is on hand for customer orders. Based on the volume throughout the line, the inventory turns about four times a year, creating a near-constant flow of materials and work throughout the facility.
While the facility has plenty of experienced workers, some of whom have been with the company more than 25 years, it takes time to train new workers at any stage of the process, including knowing what defects to spot during the inspection process for both finished leathers and anilines.
“We are not going to give the consumer anything that is not acceptable to our standards,” Kerley told Home News Now, noting that the company inspects 100% of its aniline leathers because of the color variation among the natural hides.
With the finished leathers, the percentage of hides inspected is lower because of the lack of natural variation. Regardless, the company goes through at least 20% of these hides it makes to ensure quality and consistency. “We want to make sure that when it gets out there, we are not going to have something that the consumer didn’t like or that wasn’t correct.”
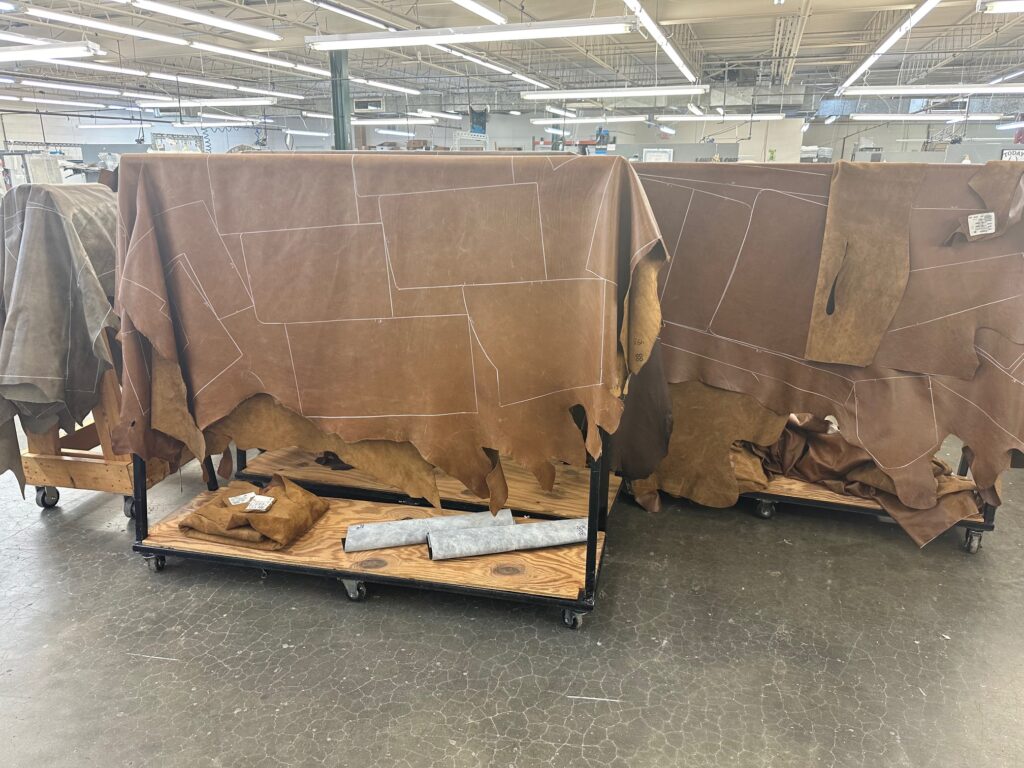
The attention to detail, including how the leather is cut and sewn, is critical as the raw material ends up being roughly 30% of the cost of the sofa. Thus, worker experience matters as it — along with the efficiencies of the Lectra cutting machine — helps ensure quality remains consistent from start to finish.
The good news for customers of the company’s domestic leather upholstery line is that the plant has workers with decades of experience, including Kerley, who has been with the company about 27 years. Many others that Home News Now spoke with onsite also had many years of experience — 10, 15, 20 years or more.

Kerley said that the plant has had as many as 80 workers and as low as 50 during his time with the company. Based on business conditions (not great, but not terrible either), Kerley said that just below 70 workers is about typical.
However as workers start to retire, the company will need to continue to bring in new and younger workers that will take time to train and learn processes that are almost like second nature to many of the people on staff now. Initially, new workers will start learning on less complex pieces such as chairs or recliners versus full sectionals which have many more parts.
“It’s hard to find anybody in this industry period, especially down here,” Kerley noted, estimating that it can take a much as a year if not longer before a sewer becomes proficient. “We’re not in the Hickory area, we’re in Cherryville and there are not a lot of other manufacturers around this way. And most of the people here have been here as long as I have. But we’ve taken the initiative and have also trained a lot of the new younger people that live in this area. We’re going to teach you how to mark, we’re going to teach you how to sew. … We’re going to teach you this because it’s not out there.”
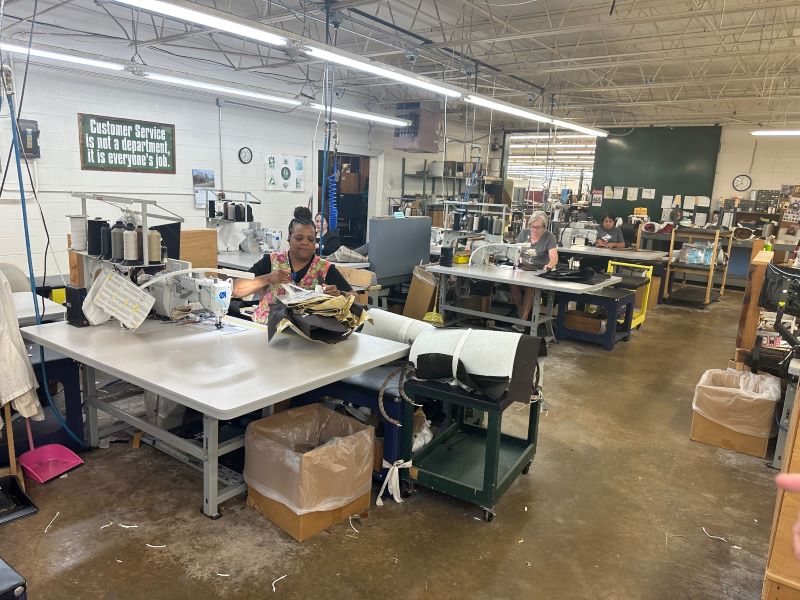
And while there may not be too much competition in the area that will steal workers away from the operation, it can be difficult to recruit employees with the same skill sets from other area employers. Regardless, Kerley noted that finding good labor is a challenge for most any manufacturer. This is particularly true as many younger workers going through college want an office or administrative type of job.
But Kerley also noted that the company has an advantage with the size, history and benefits offered by parent company Hooker Furnishings. It’s a message that the company shares in reaching out to high school students and at job fairs about the many opportunities it offers job seekers.
“This is a good and viable option for you,” Kerley said of the manufacturing jobs that exist. “You can make a really nice living in the furniture business.”