National media attention helping consumers better understand the supply chain
Just as the industry prepares for the High Point Market this month, national business news is being dominated by, among other things, the Wild Wild West of cryptocurrencies and overseas shipment delays affecting many big industries, including furniture, toys, and car parts.
Whatever lines you have to wait in during the High Point Market — for lunch, parking, or perhaps a hotel check-in — find solace in the fact that were you piloting a container-laden super freighter, there’s a good chance you would need to anchor offshore for more than a week and hope you didn’t drift back into international shipping lanes because you couldn’t even get close enough to shore to drop anchor.
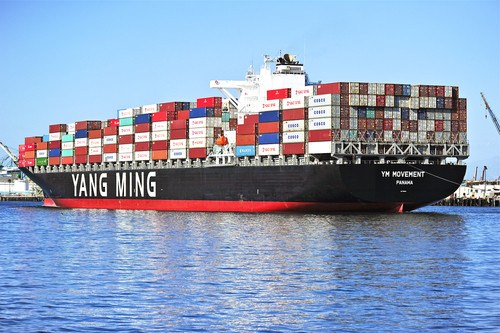
This is the situation off the coast of Southern California, where 40% of all imported goods begin their continental U.S. journeys.
According to several news outlets, a record-number of the now supersized container ships are anchored or drifting in a quasi-line awaiting their turn to dock at the ports of Los Angeles and Long Beach, the busiest port complex in the country, and getting busier all the time. The Port of Long Beach has broken monthly records in 12 of the last 13 months, according to Popular Science, while the Port of Los Angeles logged its two highest-performing quarters in its history.
The average wait time for a loading bay is eight days, and the transit time from China to the United States has nearly doubled from the pre-pandemic range of 17-28 days to now 28-52 days, according to the Drewry World Container Index.
Port congestion
On the other side of the country, the Port of New York and New Jersey complex that comprises a half-dozen sites also is breaking traffic records. Imports into this port complex of furniture, bedding, cushions, and lamps jumped approximately 35% in the second half of 2020, for example, compared with the same period a year earlier.
That these delays are making national news is perhaps a silver lining in the dark clouds of delay, Covid lockdowns in source countries, and intense competition for space on these shipping vessels. It means everyday U.S. consumers are learning more about just how complex the supply chain has been all along, and it is priming them for some sobering news at retail with respect to when they might expect delivery into their homes and the inevitable cost increases that must get passed down to them.
It also helps that so many industries are facing the same logistical challenges, which will serve to prime consumers to be a bit more patient and to expect to pay a bit more. For example, toymakers say they are paying as much as five times the normal rate for 40-foot containers to get those toys to the United States in time for the make-or-break holiday shopping season. There will be no Tickle Me Elmo this year.
Consumers are learning, among other things, the unavoidable hard costs to move goods. In 2010, a 20-foot container going from the Far East to Europe reached a cost threshold of $2,000, a sharp rise from below $500 in early 2009, according to the New York Times. This year, according to a report from Reuters, it is not unusual to pay $20,000 to send a container ship from China to the United States, though today these enormous vessels carry 40-foot containers.
Late last month, Drewry, which tracks container freight rates, reported a 19th consecutive weekly increase in the average cost to ship a 40-foot container. That average is nearly $10,000, or nearly four times the cost for the same period a year ago.
And it makes sense, because there is a finite supply of container ships — at last count, about 50,000, according to the International Chamber of Shipping. These big boats range from “small feeders” to the almost impossibly sized “ultra large container vessels” that can carry 12,000 containers. And trade imbalances inevitably mean deadhead routes back to port that add to overall shipping costs.
(Deadheading reminds me of a possible solution I pitched to a handful of furniture importers about 20 years ago: Collapsible containers. Unload, collapse the containers, consolidate and stack them, then head back to the supply side ports. It could work!)
These skyrocketing costs and burgeoning backlogs mean difficult conversations with what are a shockingly small number of big shipping lines that populate an industry infamous for its price-fixing and corruption. (You might remember the European Union’s investigation into price-fixing and market manipulation among the world’s largest container shipping companies a decade ago, or three years after shipping cartels known as “conferences” were banned in Europe and two years after a global financial crisis upended the shipping business and short-circuited international trade.)
Big Brother watching
And these challenges have drawn perhaps unprecedented attention to the oceanic shipping industry. Last month, the U.S. Federal Maritime Commission joined the European Union and the Chinese government for the fifth biennial Global Regulatory Summit. At the top of the agenda were service disruptions and bottlenecks in the ocean-linked supply chain
“The performance of ocean carriers in meeting historic demand for their services and the unusually high costs to move ocean containers are of interest and concern to regulators, legislators, and the public globally,” said Federal Maritime Commission chair, Daniel B. Maffei, stating the painfully obvious.
And back in February, President Biden took the unusual step of issuing an executive order on supply chains that initiated an inter-agency review of vulnerabilities in sourcing to guide policymaking. Unfortunately, the review likely won’t be completed until early 2022.
Glass half-full?
Of course, many furniture companies would love to trade for the problem of waiting on container ships to matriculate through the various U.S. ports and onto trucks. Production stoppages related to Covid infection rates in Vietnam, Malaysia, and China continue, and the effects on cash flow are rippling up and down the supply chains as payment schedules and terms are thrown out the proverbial window. This means that getting the furniture onto ships headed for Southern California is increasingly problematic.
Chinese ports at Nigbo-Zhoushan and Yantian, which are among the world’s busiest, saw partial shutdowns related to Covid virus outbreaks. At a time when raw material costs are climbing as much as 20 percent, ship times are up from China nearly 80 percent. To borrow from the language of the seas, global logistics have run into a perfect storm of negative headwinds and choppy waters.
Perhaps the brightest shine in the multi-faceted silver lining comes from the U.S. economy and consumer buying power and appetite. The director of the Port of Los Angeles told CNN rather bluntly that the “American consumer’s buying strength is so strong and epic that we can’t absorb all this cargo into the domestic supply chain.”
To this “epic” description of U.S. consumers eager to snap up whatever is available in stores, especially those selling online, add the good news that furniture manufacturing doesn’t require too many semi-conductors and that furniture retailing isn’t subject to the rodeo bull-riding of cryptocurrency fluctuations. At least not yet.
Wishing all a productive October market!
One thought on “Blog: A silver lining in the dark clouds of shipping delays”