CONOVER, N.C. — Four years ago, the team at Universal Furniture had no idea their upholstery division would one day help them weather the storm of a global pandemic.
Back then, the move to launch an in-house upholstery operation just seemed like a logical next step as the company ramped up its to-the-trade business. The division eventually expanded to 350 SKUs, with motion and leather options available. But as Universal’s designer demand grew, so did the need to be able to accommodate special orders.
So in fall 2019, Universal’s parent company, Samsung Holdings, acquired Conover, N.C.-based Southern Furniture. Southern had a 400,000-square-foot upholstery plant in Conover, the ideal setting for Universal to invest in its upholstery business. The company started efforts to revamp the outdated factory, and added additional workers to help shoulder the burden of growing orders.
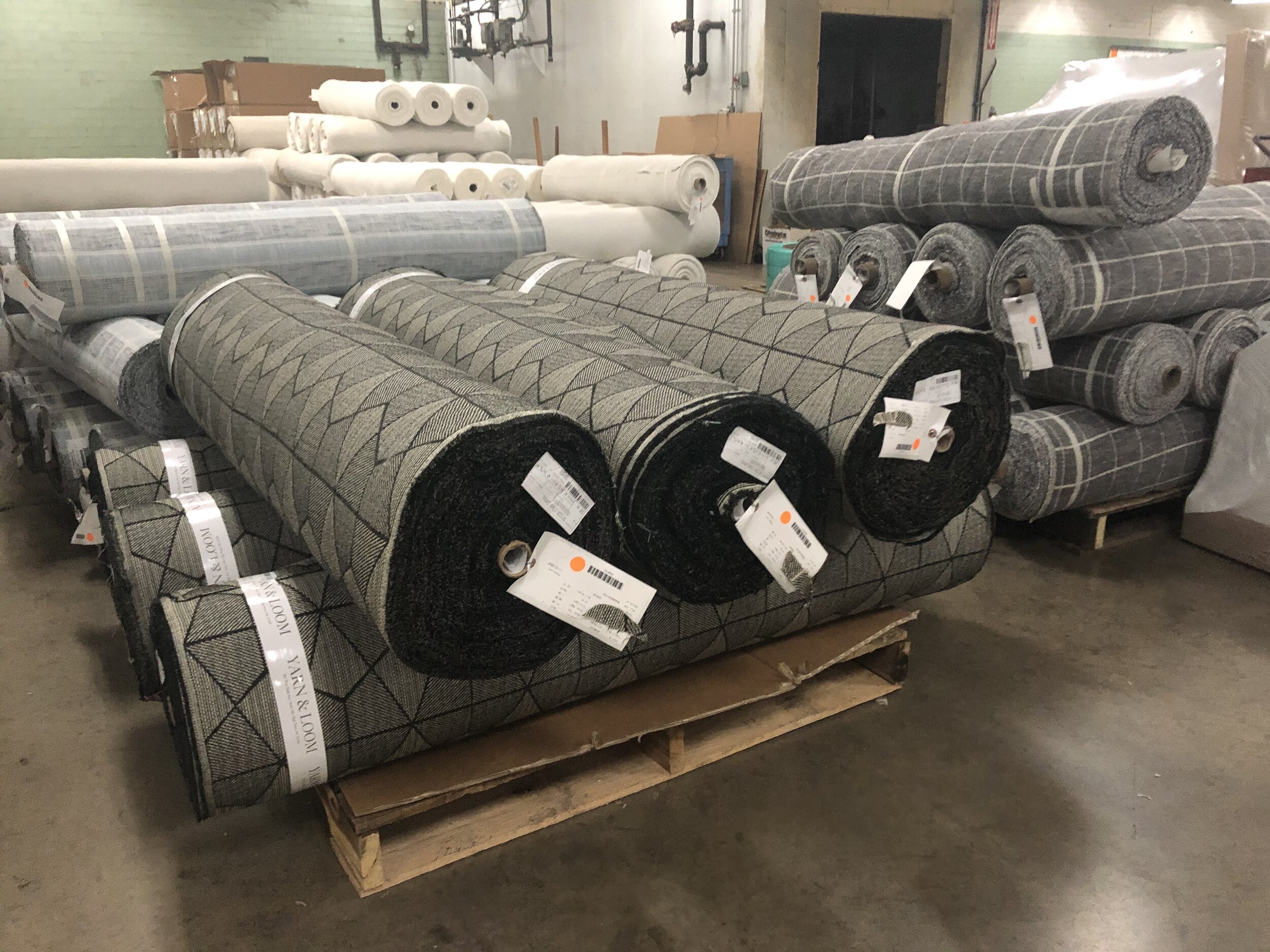
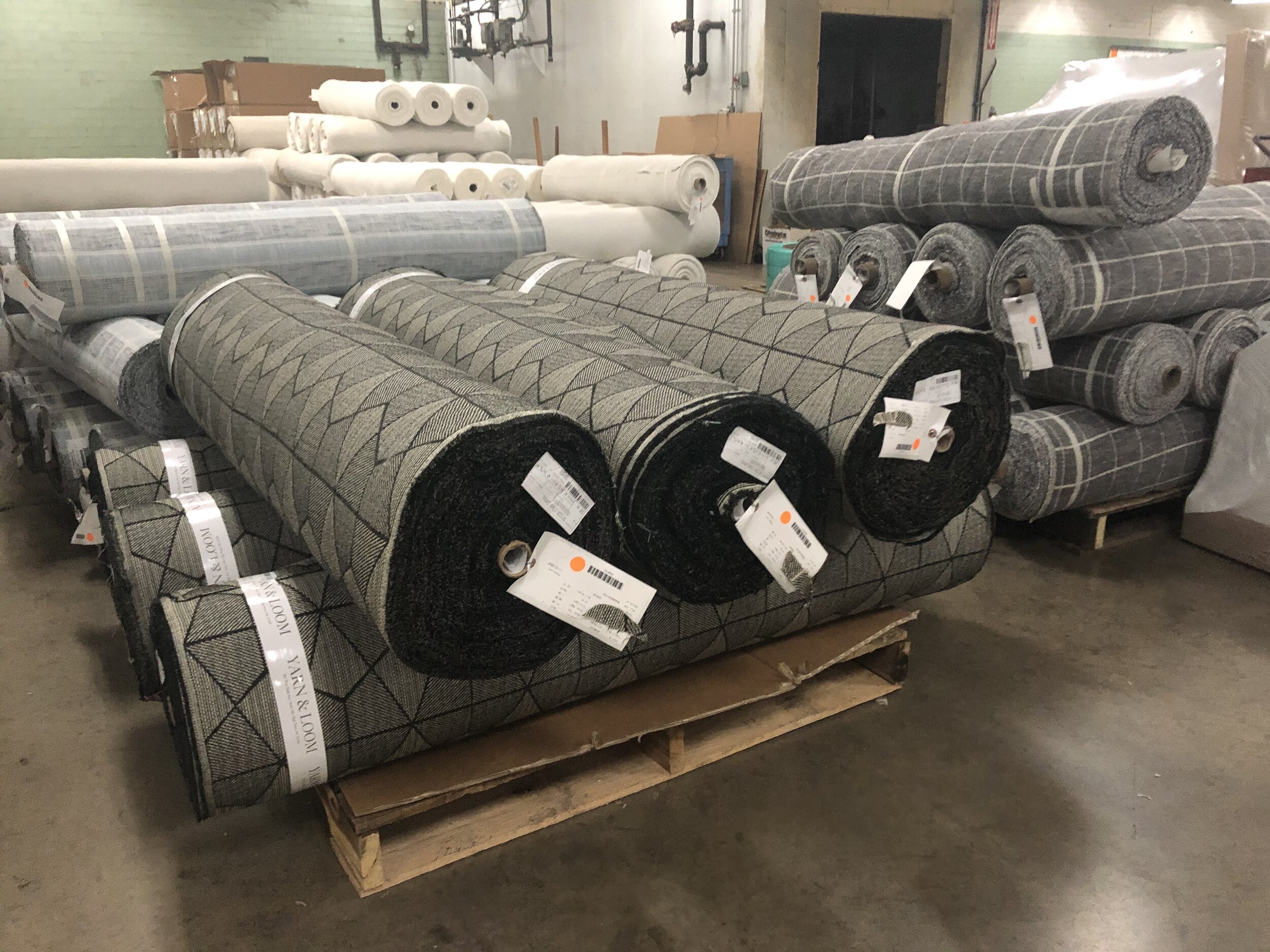
Universal offers more than 400 in-stock fabrics for special order upholstery.
Then COVID-19 happened.
As manufacturers shut down operations around the globe and retail business ground to a halt under stay-at-home orders, the future of the furniture industry seemed uncertain. But as restrictions began to ease in May and June, furniture retailers were suddenly inundated with business from consumers eager to revamp the homes they’d been trapped in for the previous months.
With that demand on the heels of two months of inactivity, many furniture producers found themselves buried in a backlog of orders, complicated by logistical issues and shortages of materials like fabric and lumber.
But while Universal temporarily shut down production during the early days of the pandemic, they continued building their fabric inventory to be ready to launch once things calmed down.
“Because we were planning for special-order business, when everyone else shut down and stopped buying, we kept buying because we were anticipating this business and special orders, and that put us in a better position,” said Sean O’Connor, senior vice president of sales, Universal.
var gi_protocol = document.location.protocol;
var gi_redir = “”;
var gi_dasrc = gi_protocol + “//display.hcgmedia.com/?dsid=548202072085523523&pid=329&skid=76&if=0&at=0&alid=728_90&adtype=0&exty=1&special=0&redir=” + gi_redir + “&r=” + Math.random();
document.write(“”);
var gi_protocol = document.location.protocol;
var gi_redir = “”;
var gi_dasrc = gi_protocol + “//display.hcgmedia.com/?dsid=57420208119551504&pid=329&skid=76&if=0&at=0&alid=728_90&adtype=3&exty=1&special=0&redir=” + gi_redir + “&r=” + Math.random();
document.write(“”);
Now Universal has 425 fabrics and 50 leathers available (the latter mostly sourced from Moore and Giles) to cover frames they source from two local companies. O’Connor said there have been some challenges launching this operation in the midst of a pandemic, but it has also presented opportunities.
“We are launching the business in the middle of COVID and haven’t been able to be exposed to the amount of people we want,” said O’Connor. “But then because our business is so new, and we’re just ramping up, we’re able to get product out in 6-8 weeks.”
O’Connor said they have the ability to do COM for designer orders, as well, but they’ve put that temporarily on hold to keep up with demand for in-stock fabric orders.
Managing that growth has been a big push for Universal. When they moved into the Southern plant late last year, they found it hadn’t really been updated in more than 50 years. Since then, the company has invested in new machinery, upgraded lighting and cosmetic fixes like new paint, all while reworking production floor layouts to increase efficiency.
Incorporating technology has been important, too. The company plans to bring in new cloud-supported machinery, and each sewer on the line will be outfitted with an iPad at their station that automatically downloads and updates patterns.
“I’m not aware of anyone in the industry using iPads at sewing work stations,” said Dale Smith, general manager of the facility. “So our quality will improve because we’ll get it right the first time—every sewer will have that at their fingertips, so they’re much more efficient.”


Sewers in the Universal upholstery facility can easily access patterns via iPads at their work stations.
And while Universal is making significant investments in equipment, it also wants to add people to the operation. O’Connor and Smith said the plant is actively hiring positions throughout the facility, and they’d like to add 50-60 more employees by the end of the year.
“We’re ready for things to move more efficiently, but our backlog is growing, and we have to infuse this place with more manufacturing talent,” said O’Connor.


Universal is actively recruiting skilled workers for its Conover upholstery facility.
That backlog is due in part from early buzz for the upholstery line from the summer High Point mini-market and the fall High Point Market. The launch of the company’s Coastal Living Outdoor line—which includes outdoor-safe upholstered pieces—has led to additional orders, as well.
“We still haven’t had the line exposed the way we’d like to, but we signed on 300 retailers in the first 30 days, and we’ve accumulated 600 retailers and designers in the first four months,” said O’Connor.
In the meantime, O’Connor said Universal will continue to focus on growing the operation to provide designers and retailers special order product as quickly as possible—a major advantage in a time when orders are so delayed due to COVID.
“Our goal as a business is to be the easiest company to transact with,” he said.
var gi_protocol = document.location.protocol;
var gi_redir = “”;
var gi_dasrc = gi_protocol + “//display.hcgmedia.com/?dsid=578202081881555635&pid=329&skid=76&if=0&at=0&alid=728_90&adtype=3&exty=1&special=0&redir=” + gi_redir + “&r=” + Math.random();
document.write(“”);
var gi_protocol = document.location.protocol;
var gi_redir = “”;
var gi_dasrc = gi_protocol + “//display.hcgmedia.com/?dsid=582202091474319419&pid=329&skid=76&if=0&at=0&alid=728_90&adtype=3&exty=0&special=0&redir=” + gi_redir + “&r=” + Math.random();
document.write(“”);
var gi_protocol = document.location.protocol;
var gi_redir = “”;
var gi_dasrc = gi_protocol + “//display.hcgmedia.com/?dsid=5892020108184154614&pid=329&skid=76&if=0&at=0&alid=728_90&adtype=3&exty=1&special=0&redir=” + gi_redir + “&r=” + Math.random();
document.write(“”);
var gi_protocol = document.location.protocol;
var gi_redir = “”;
var gi_dasrc = gi_protocol + “//display.hcgmedia.com/?dsid=566202081191214486&pid=329&skid=76&if=0&at=0&alid=728_90&adtype=3&exty=1&special=0&redir=” + gi_redir + “&r=” + Math.random();
document.write(“”);
Alot if what Dale smith said is not true. Southern had already updated the lights before he came to universal, they only put new paint 8n the sewing dept. And only do upgrades in the sewing dept. Leaving everyone else out.
I worked there and I received covers straight out of sewing and it definitely was not done the right the first time. I would say about 50 to 60% of our covers had to be sent back to be redone.