In mid-January, Home News Now visited Gat Creek’s Berkeley Springs, West Virginia, plant, which has been expanded by 40,000 square feet for a total of 140,000 square feet. The company invited the publication on an exclusive tour of the facility, which dates back to 1972 when it originally operated as Tom Seely Furniture.
Purchased by Gat Creek CEO Gat Caperton in 1996, the business underwent its first expansion in 2005. This latest expansion, which began just over three years ago, was fueled by demand during the pandemic. Lead times which rose to about 23 weeks during that period of high demand have now come down to a more typical five weeks.
As part of our coverage of the recently completed expansion, we took a tour of the facility to get a first-hand look at the machines and people that bring the company’s case goods line to life. The images below capture some of that dynamic, which continues the company’s legacy of being one of the remaining producers of solid wood furniture left in the United States.
We also have included here a video interview that Editor-in-Chief Tom Russell did with Caperton at the plant, in which he explains the significance of this latest expansion for the company and its customers.
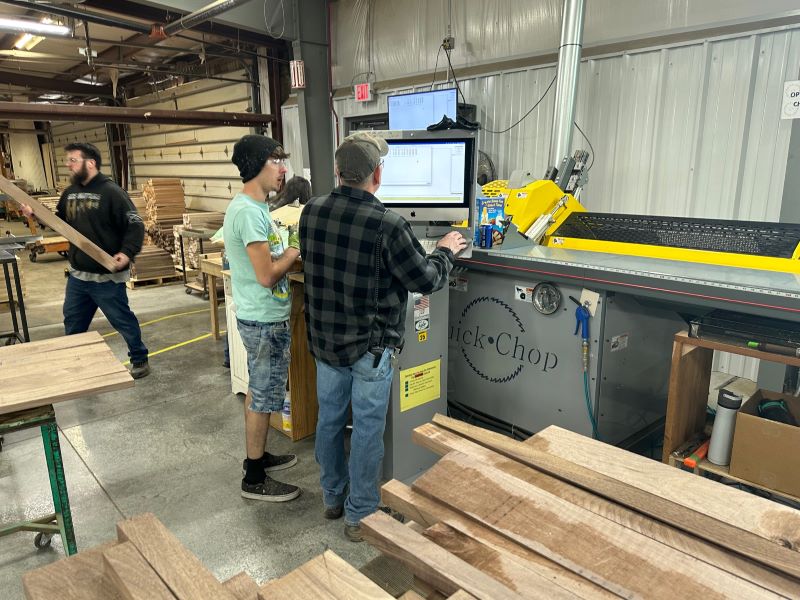
This optimizing rip saw helps to maximize the yield of lumber that comes into the Gat Creek plant each week to be used in the production of solid wood furniture.
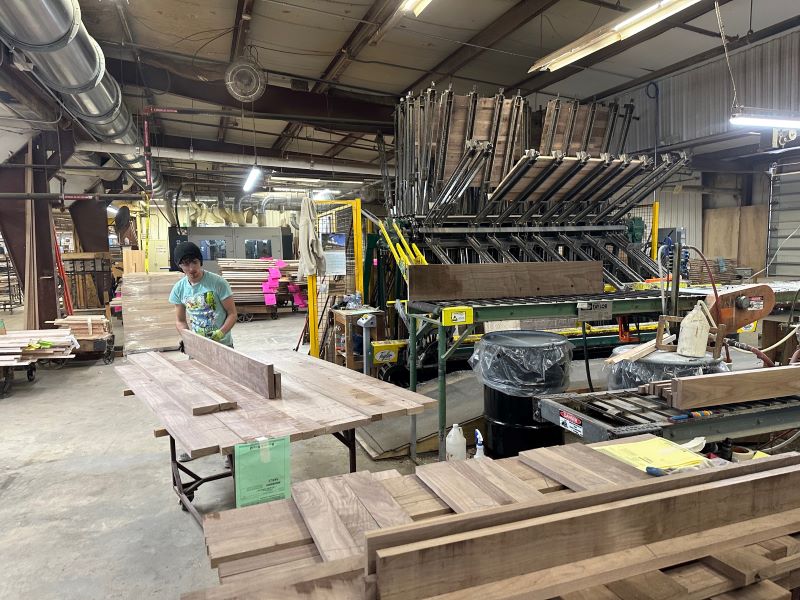
Inside the Berkeley Springs plant, a worker selects wood panels to be glued together in the clamp seen in the background.
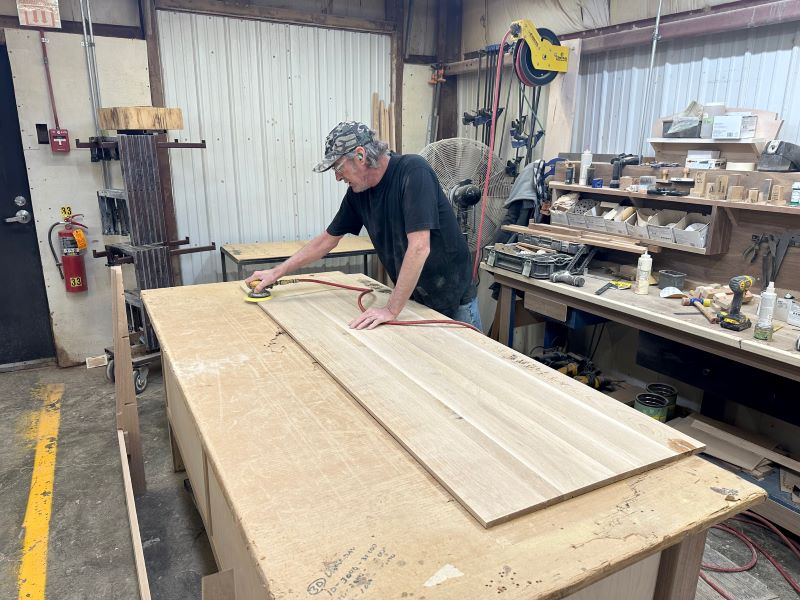
David Gray is seen sanding panels that have been glued together. This is an important part of the production process as it prepares a smooth surface for wood finishing.
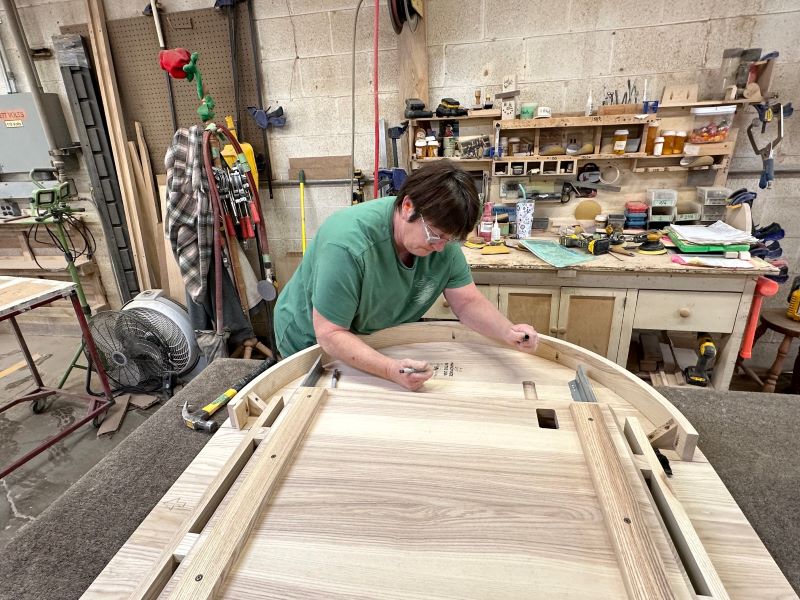
Thirty-year Gat Creek employee Angie Robinson signs the bottom of a table she has helped assemble.
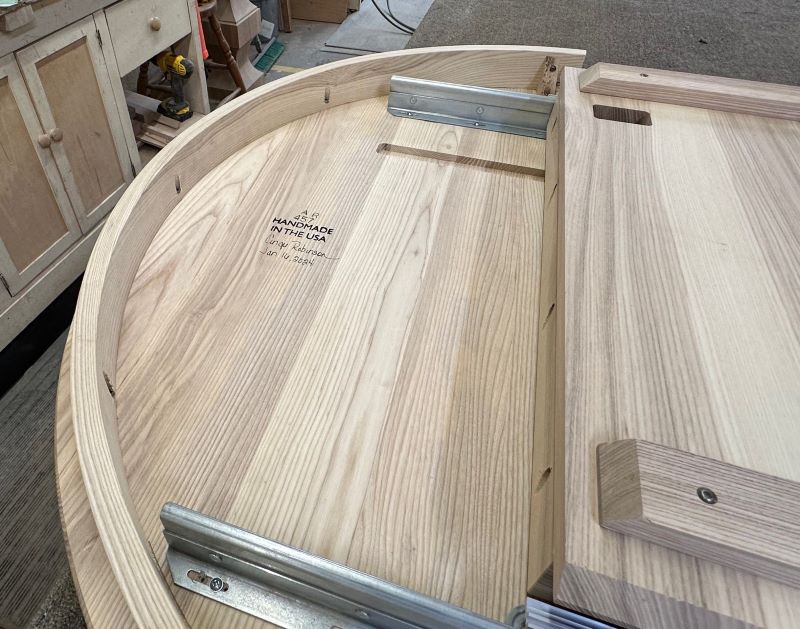
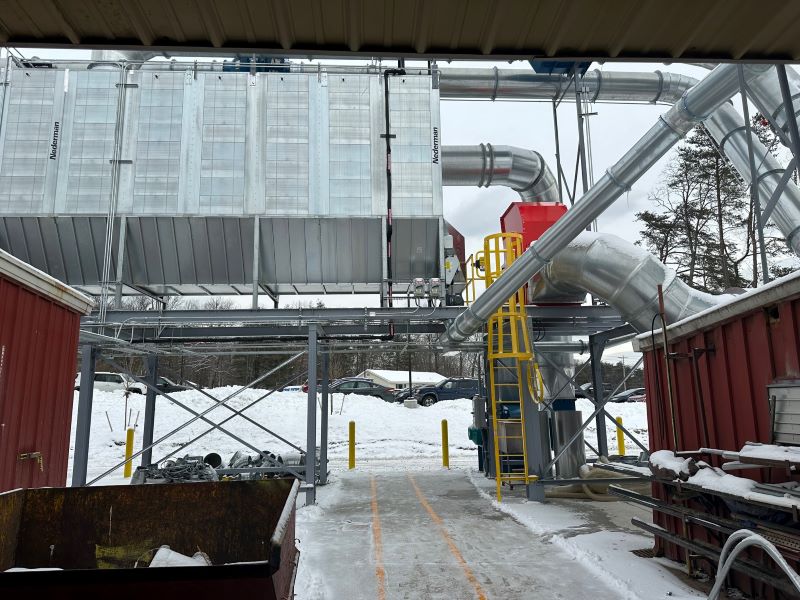
This new dust collection system replaced a previous 50-year-old system at the plant at a cost of about $1.5 million.
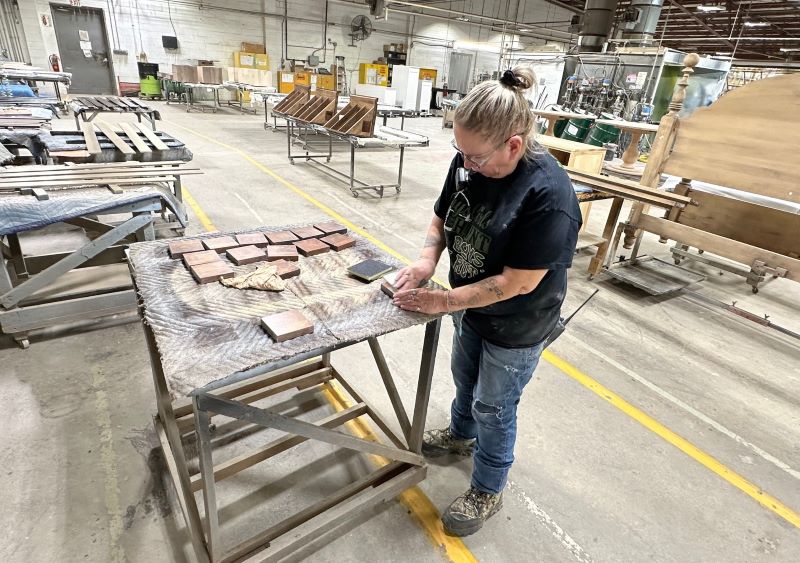
Stephanie Stotler, a 39-year employee of the company, is seen preparing finish panels used as part of the presentation to customers.
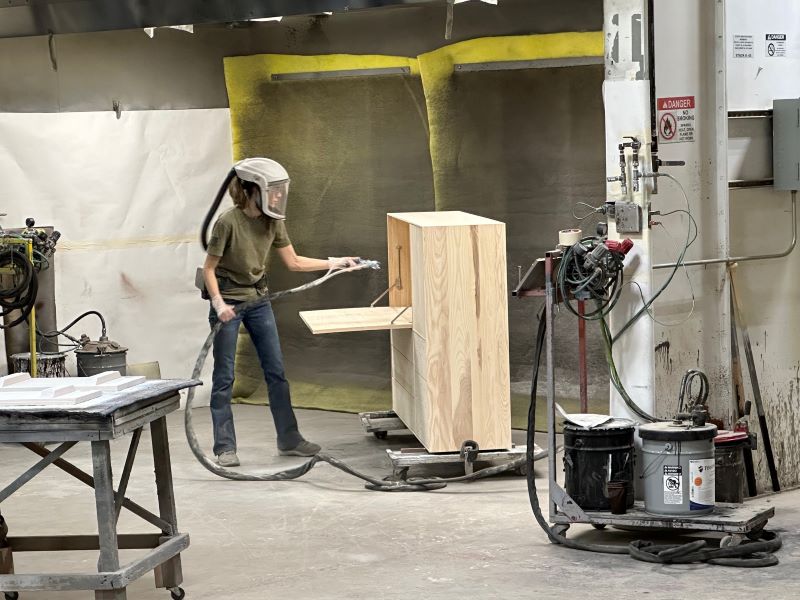
Finishing is an important part of the nature of Gat Creek’s custom business and remains a core capability of the Berkeley Springs plant.
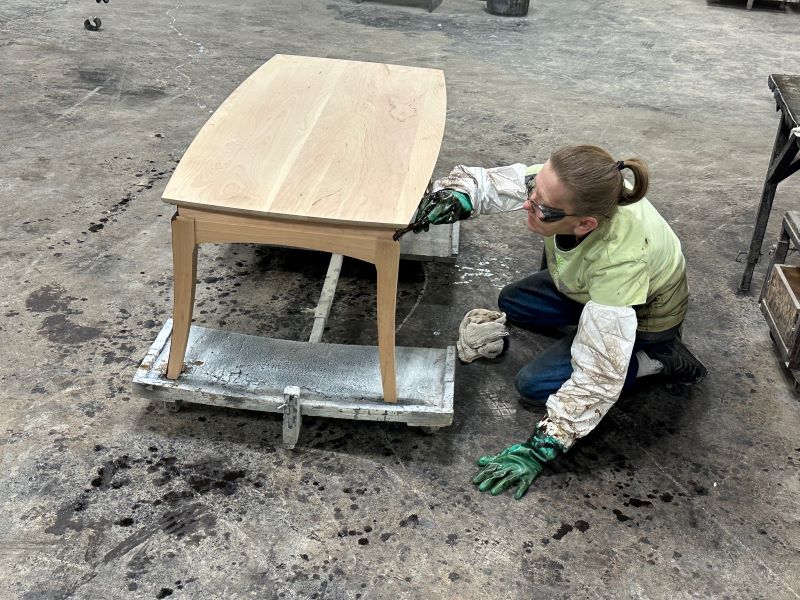
Teresa Miller is seen hand-applying finish to a cocktail table, part of the process that involves the skills of a multi-talented workforce.
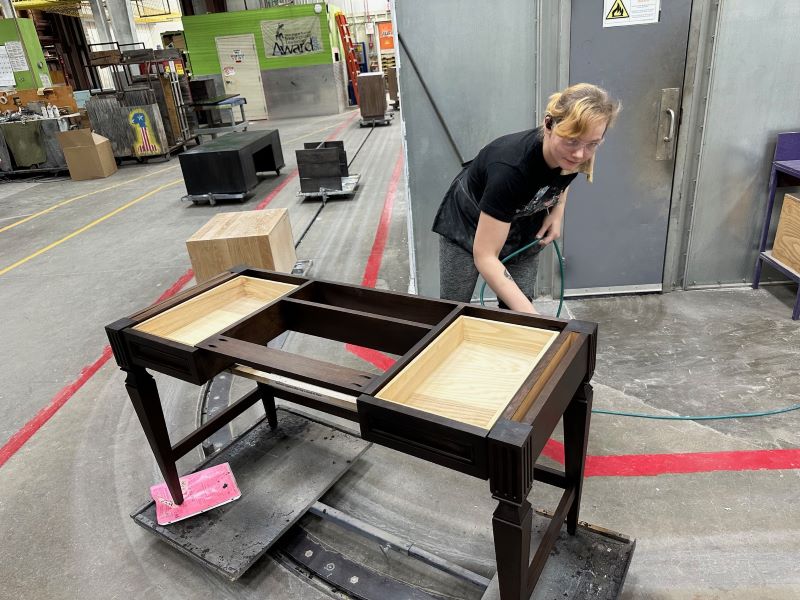
Breanna Harman is seen getting excess dust off a desk that is being finished at the plant.
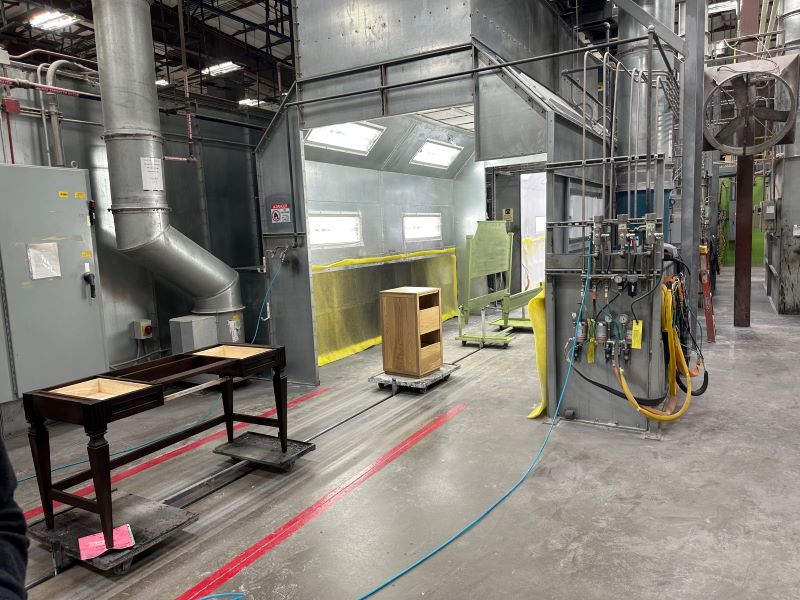
Pieces are seen traveling into a finish booth, one at a time, illustrating the made-to-order, custom nature of the Gat Creek line.
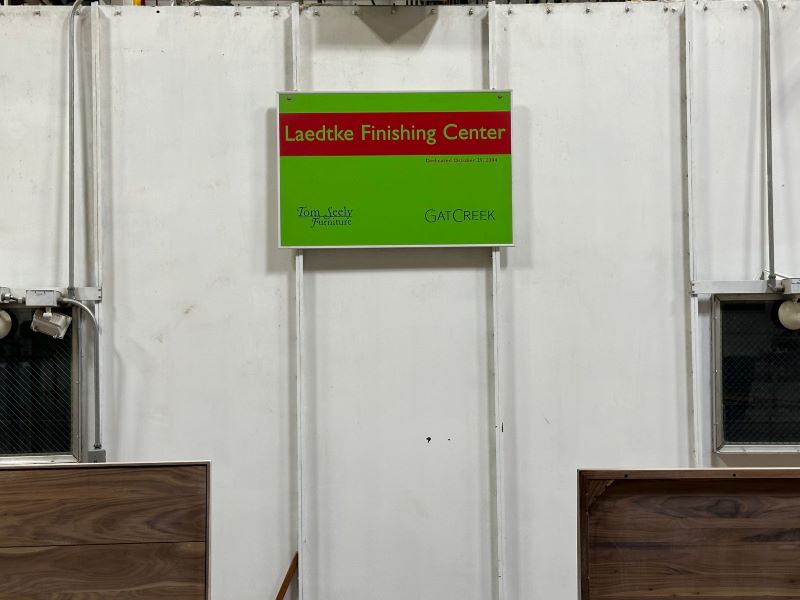
The company’s first finishing booth is dedicated to long-time Tom Seely and Gat Creek customers Bud and May Laedtke, of Village Antiques and Reproductions of Chantilly, Virginia. Caperton described them as “great customers and heroes of World War II.”
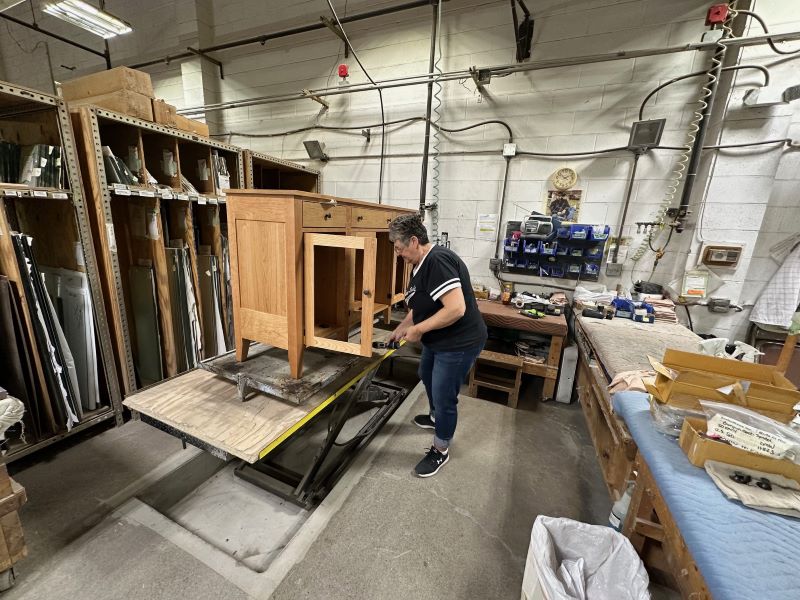
Sixteen-year Gat Creek employee Beverly Kesecker is seen installing hardware, shelves and glass in a the Berkeley server, designed by Gat Caperton.
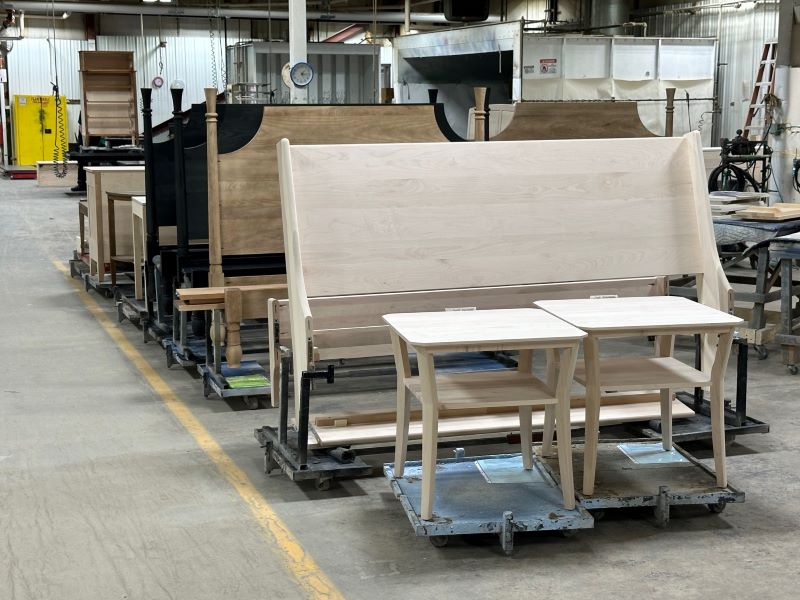
Various headboards, accent tables and case pieces are seen on the plant floor awaiting final finishing.
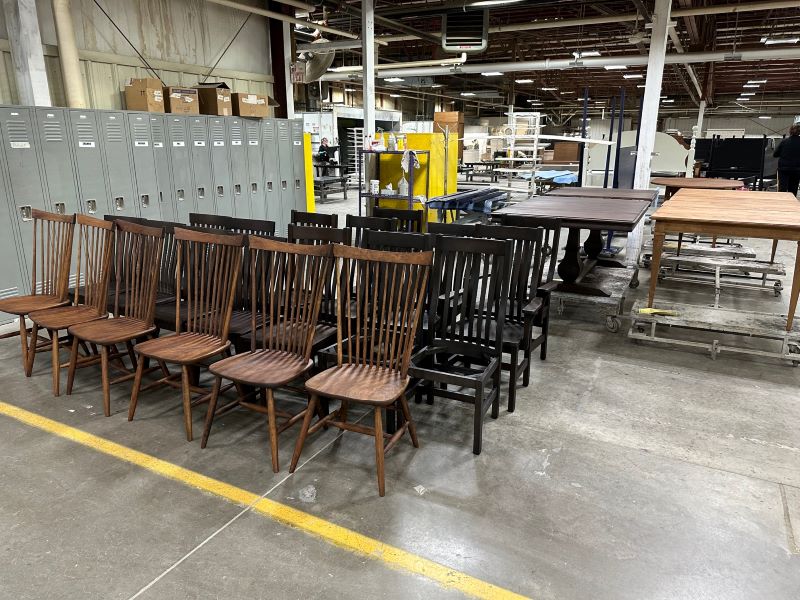
These are some of the chairs and tables produced by Gat Creek Furniture. Once completed, they will be packed and shipped from Gat Creek’s shipping area, which also was expanded as part of the multi-year project.
Nice article and video presentation. Always good to see goods made in America.
Good to see valued employees wearing protective safety gear,not always seen in factory videos or visits today..
Wish Gat Creek the best.