Case goods manufacturer says it can further reduce lead times by remaining focused and adapting its product line to the capabilities of its plant
GOSHEN, Ind. — Case goods manufacturer Foundry39 is working toward a goal of cutting its lead times by more than 80% by adapting its product line to the capabilities of its manufacturing facility over the next 12 months.
The company currently produces its made-to-order line of solid wood TV consoles, desks, occasional tables and credenzas in 30-40 days from the time of order.
But at a time when customers are seeking quicker turnaround and delivery of finished product, company President Chad Gascho said that’s too long a window. Now he wants to reduce that to as little as five to seven days (weekends included).
“Our goal is to push our lead times down to a week,” he told Home News Now. “We can do it and we are going to do it.”
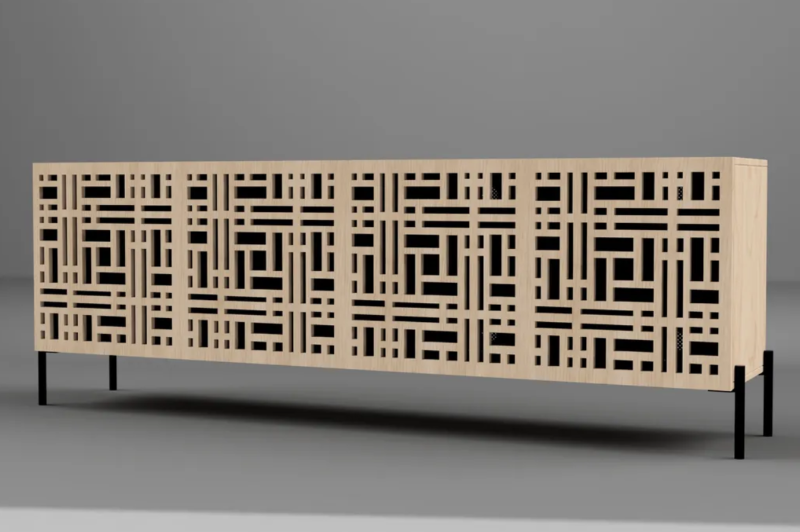
But for Gascho, that drastic a turnaround is not just wishful thinking. He’s seen it in practice from another Goshen, Indiana, company called Viewrail. It produces and delivers custom floating stairways in as little as 10 days.
Gascho said he met company owner Len Morris a few years ago and learned that their companies were similar in many ways. For one, they each were startups that previously dealt mostly with Amish producers. Second, they each produced a custom line. Third, they each produced a line from solid wood components.
“They make stairways and every single one is custom as you can imagine as everyone’s house is different,” Gascho said. “And as complicated as that is, they can deliver it to a customer in 10 days. … I said ‘if you guys can do what is ultra-complicated in 10 days, why can’t we do it in five.’”

Gascho pointed out that Foundry39 also is a young company that can make the transition to lower lead times easily because of the nature of its production. He first established the Foundry39 line of TV consoles in late 2017 as part of Conrad Grebel, a bedroom and dining producer he sold to LJ Gascho Furniture in Pigeon, Michigan, in 2021.
Chad Gascho purchased Foundry39 back from LJ Gascho as a way to keep its 10,000-square-foot plant in Goshen, Indiana, running and thus keep its half-dozen workers employed. Last summer, the line expanded to desks, credenzas and occasional tables, and currently has about 100 SKUs including at least a dozen TV consoles.
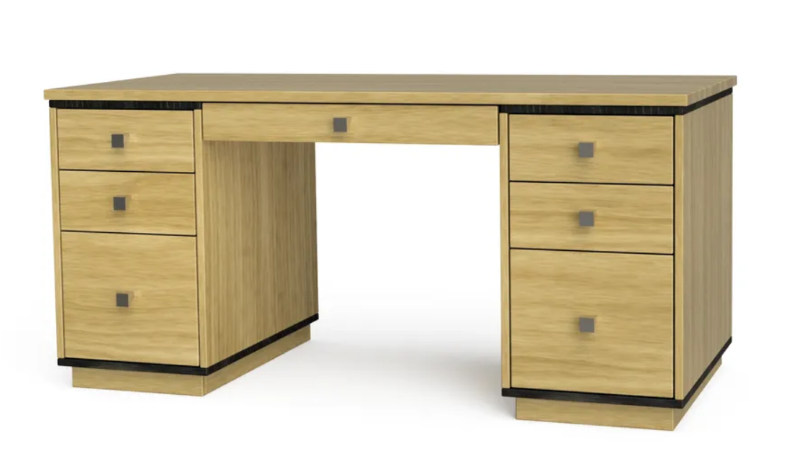
“We had to develop new product other than TV stands,” Gascho said. “It wasn’t enough of a category. So home office, occasional and the sideboards were created at the same time, which would have been in August of last year.”
Looking for someone to help with the transition to lower lead times, Gascho went to Morris, of Viewrail, for some suggestions. One of the names he passed along was Will Walters, one of the original operations professionals at Viewrail when it first started. Walters is now the recently hired director of operations at Foundry39.
With Walters at the helm of operations, Gascho is confident the company will achieve its goal.
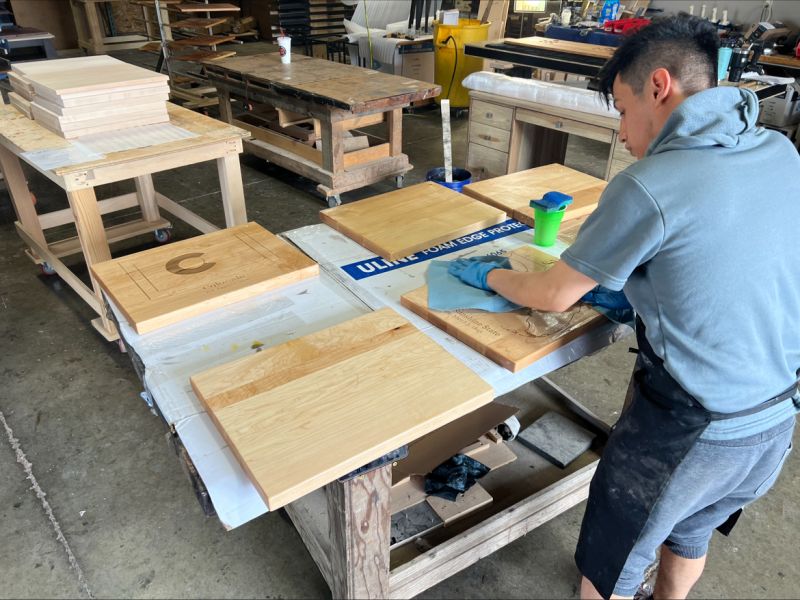
“Yes, we are going to get there,” he said, basing that on Walters’ assessment of both the product line and the way the plant is set up. Gascho noted that the line itself complements the capabilities of the plant, meaning it will build the product based on its attributes not the other way around where the plant has to be reconfigured to build an ever-changing product mix. “It was about the way that the flow was already set up and what we were building — that is really what he (Walters) really saw and he said, ‘Chad, no problem.’”
“It is very lean,” Gascho said of the way the plant is set up, noting that the process is very streamlined from the cutting of woods to various thicknesses and widths to the creation and gluing of panels and on to sanding, finishing and assembly.
The plant itself is relatively small, which may cause some to pause relating to its overall capacity and ability to turn out goods in high volume compared to larger plants in and outside the U.S. However, Gascho said that is not a negative as the plant will grow with new equipment and space as needed.
“Our shop is really not that impressive,” Gascho said of the overall 9,000 square feet of manufacturing space. “That is the amazing thing behind it. It is more about the flow and what you are building and how you are building … and the flow to actually create it.”
“Being lean, the goal is not to sit on inventory, which takes up space,” he added. “At some point we will have to (expand), but right now we know we can push a lot of volume out of this small facility if it is just going out the door and not sticking around. We are not in a hurry, but will certainly do it when the time comes.”
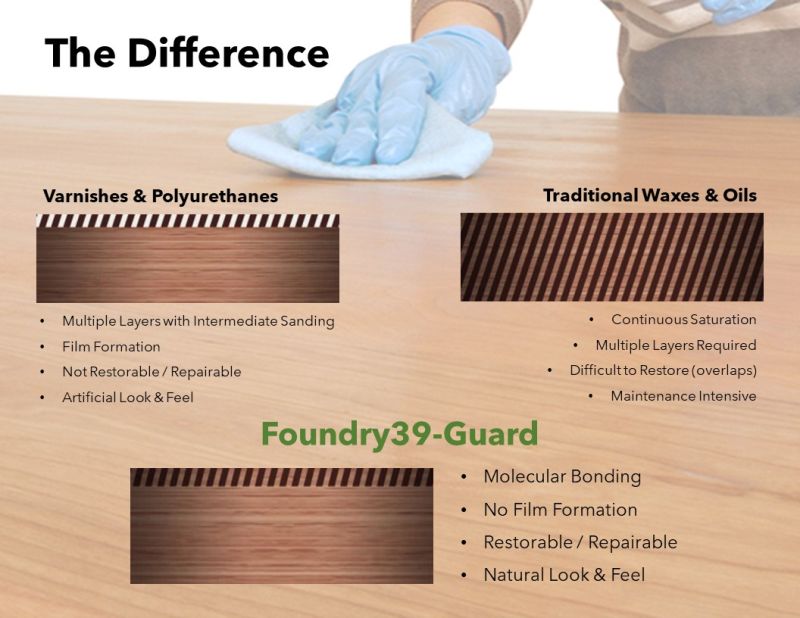
Gascho also touts the finishing capabilities of the facility. It works with an environmentally friendly, plant-based non-volatile organic compound finish called Foundry Guard that gets applied to components before they are assembled, Gascho said, noting that the process ends up being faster than traditional finishing methods. He also explained that compared to a more typical conversion varnish or lacquer that coats the surface, this finish bonds with the wood grain.
“It actually becomes part of the wood instead of it just being a coating that just goes on top,” he said. “So it is infinitely more durable.”
Gascho noted that the company’s still relatively young age has allowed it to incorporate these various methods with relative ease compared to a company with a longer history trying to incorporate various changes into its processes. Thus he believes its flexibility will serve its customers well as it seeks to achieve quicker turnaround times.
“Time demands and speed are going to become the norm, so we as manufacturers have to adapt to that,” he said. “We have the blessing of being new enough in that we were able to flex very early on and adapt to it.”