A panel of experts at last month’s Furniture Manufacturing Expo offers insights into investing in technology and balancing equipment needs with human talent
HICKORY, N.C. — A panel of engineering experts at last month’s Furniture Manufacturing Expo held here talked about the importance technology has played in their manufacturing operations while also highlighting some of its limitations in producing custom product.
A key message was that while certain advanced equipment can handle the jobs of several people, human hands and minds are needed to operate the equipment and also to perform tasks such as building, assembling, finishing and upholstering the pieces — not to mention sewing fabric.
The panel, moderated by Tom Russell, editor-in-chief of Home News Now, included four manufacturing experts in the field: Evan Drum, director, engineering, Bassett Furniture; Drew Dilsaver, CNC manager, Sherrill Furniture; Keith Nichols, vice president, manufacturing at Century Furniture and Dale Smith, general manager, Universal Furniture.
These experts provided an overview of some of the advances in technology their domestic plants have made in recent years, both in upholstery and case goods, allowing them to ship product more quickly and efficiently to their customers.
In addition to improving efficiencies in manufacturing, the equipment has addressed another issue that may not have been as pronounced as when they first acquired it: labor shortages that have become more acute during the pandemic.
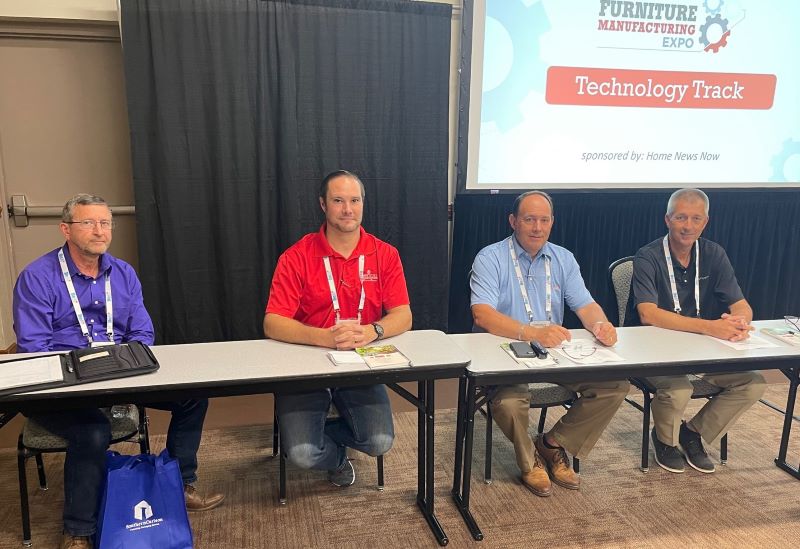
Thus, certain machines have been able to perform the jobs of several people, allowing plants to get certain tasks done with less workers. This not only helps eliminate the time-consuming task of finding workers for certain jobs; it also has allowed the plants to reassign individuals to other tasks where they can add value to the production process.
Some 30 years ago, Bassett Furniture, for example, had some 160 people in its machine room and rough mill, Drum noted. Today, thanks to advances in technology, it is producing more frames with fewer workers.
“The non-value-added labor is gone,” he said. “We had 160 people back there, and we are now cutting with 20 people now probably twice the frames we did with 160 people.”
The experts noted that investments in equipment have been particularly important in recent years due to spikes in demand that have raised backlogs to historic levels.
“When unemployment is 3.5%, you just can’t get people in the door — there is not much you can do,” Drum noted. “You have got to…simplify what you are doing and to engineer labor out of it… We are all battling for the same people, so I am glad that we invested the money to get better sewing machines and better equipment prior to this whole backlog situation or we would be in a mess. And we are doing what we can to knock it down.”
Others agreed that investments in equipment have helped manage the backlogs.
“Our incoming order rate for the last two years has been at a level that — even with automated cutting machine equipment and CNC routers — there is not enough time in the day to make the product and the orders that are coming to us,” said Century’s Nichols, noting that without the equipment, the backlogs would be even higher.
Of the company’s automated fabric cutting equipment, he noted that each machine probably replaces seven to eight cutters. Without that equipment, he said the company would probably need 30-35 more cutters to sustain its current production levels.
“Considering the fact that you need growth, you need to do more, and finding that extra labor is difficult,” he added. “It is not impossible but the labor market is very constrained so the technology we have invested in not just over the last two years, but over the last 20 years, 25 years and even 30 years has certainly allowed us to sustain our production levels and allows us to grow them.”
Dilsaver, of Sherrill, agreed that it would be difficult to manage backlogs without advancements in technology.
“It would actually be a tremendous undertaking at this point,” he said, adding that the demand for customization has continued to make people a critical ingredient in the manufacturing mix. “People always say “do more with less, do more with less…We are not trying to do more with less… What we are doing is trying to do more with the same. We are not trying to eliminate people or drop them out of our mix. What we are trying to do is reprioritize their jobs.”
Drum, of Bassett, said that the increased backlogs have also resulted from snags in the supply chain that have held up everything from brackets and mechanisms to plywood. Yet here too, investing in technology has helped better manage the process.
“It is always something slowing you down that has kept the backlog where it’s been,” he said, noting that challenges getting good labor also has impacted suppliers. “But had we not taken advantage of technology prior to this, we would have been in dire straits.”
The manufacturing experts also see technology as a recruitment tool for the next generation of workers needed to fill certain jobs.
“Absolutely,” said Dale Smith of Universal, of whether technology can be a way to get younger people interested in furniture manufacturing jobs.
“Technology is the wave of the future, it’s got to be,” Smith said, noting that it can help “entice young people to come in and give them a challenge that they can adapt to. Not everybody can upholster. Not everybody can run a sewing machine. But if somebody can operate a router … or can get the right end result by drawing something out in CAD and getting it into a cutting machine that gets the right product out — some people find a great deal of satisfaction in doing that. Thank God they are there.”
Even if unemployment rises — and backlogs come down — officials still believe they will still need to fill certain positions, whether they’re in custom finishing, running a CNC router or operating advanced fabric or leather cutting machinery.
“Finding good quality people is still the challenge,” Smith said. “You want the best person that you can possibly get… But technology is one of the main highways we’ve got to stay right in the middle of to get those people in.”
Given the highly customized nature of upholstery and case goods manufacturing, Sherrill’s Dilsaver agreed that finding the right people with the right skills will be a balancing act moving forward.
“Technology is limited by the rules we have given it,” he said. “So it has to live inside those confines… You still have to have some of those people elements. Does a computer know how well a chair is going to sit? It can take pressure points and calculate what it is but everybody here probably knows somebody at the company with the golden hind end that can sit down in it and then stand up and tell you if it is good. Or not.”
“So we still need those people in that area,” he added. “And with things being so much customized … where everything now is how you want it, we are short-order chefs and we are not making things lock, stock and barrel … Everything is so customizable that it makes it more difficult to automate that entire process. When it comes to things being sewn, you still need a person who is pulling the right fabric or putting it on there or making that repair judgement based on what’s going on.”
Nichols, of Century, agreed that the custom nature of the domestic industry indeed requires a human element. However, he believes that the industry and its equipment vendors can find new and innovative ways to automate the process.
“We have to continue to push that envelope and to continue to ask for those things,” he said, adding, “That is what we have to do as an industry — to expand technology even further into those jobs we think will never be automated.”
Smith, of Universal agreed that the industry needs to continue to innovate in the area of technology, getting vendors to think outside of the box with their own product development.
But he also agrees that the industry needs to keep developing human talent and finding new ways to continue drawing those individuals to the industry.
“I think that the most critical thing right now besides technology is to be able to attract those people into our industry,” he said, noting that when much of the case goods business left the U.S. more than 25 years ago, a lot of people who lost their jobs discouraged their children from getting into the business.
“It is hard to find those skill sets any more because it is gone,” he said, referring to the case goods side of the business. “But on the upholstery side, there is a lot of opportunity and I have some upholsterers making darn good money. You have to have some benefits that will appeal to the younger group of people, but that is the most important thing we have to do.”